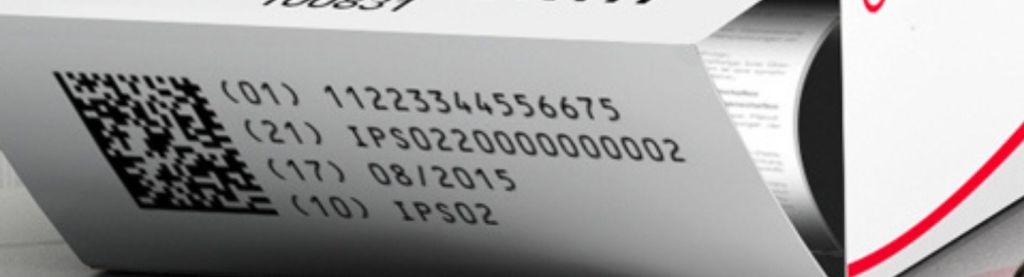
PHARMA-CODE Series: #2 PHARMA-CODE Printing
In a previous article, we explored how PHARMA-CODE is similar and different from other barcode types. Now we invite you to explore with us the practicalities of printing the PHARMA-CODE on your products. With other barcode types, it is always a critical concern from the printer suppliers about validating the data structure. The certainty that the encoded information is correct is an essential aspect of barcode quality with external usages (open-loop) barcodes such as GS1 and HIBC UDI. This is not a concern—or at least not the printer’s concern—with PHARMA-CODE because it serves in an internal usage (closed-loop) application. Part 1 of our PHARMA-CODE series explains this in detail.
PHARMA-CODE number allocation
The sole purpose of PHARMA-CODE is to ensure that only the correct collateral information is included in a pharmaceutical package. The package itself and all relevant inserts must match. The product manufacturer allocates the PHARMA-CODE numbers for this purpose. Lookup to a database is not necessary, so a standardized numbering protocol is not required. On an assembled package, the PHARMA-CODE barcode is no longer visible.
Consumers and pharmacies often pay little attention and even not aware of the existence of those PHARMA-CODE.
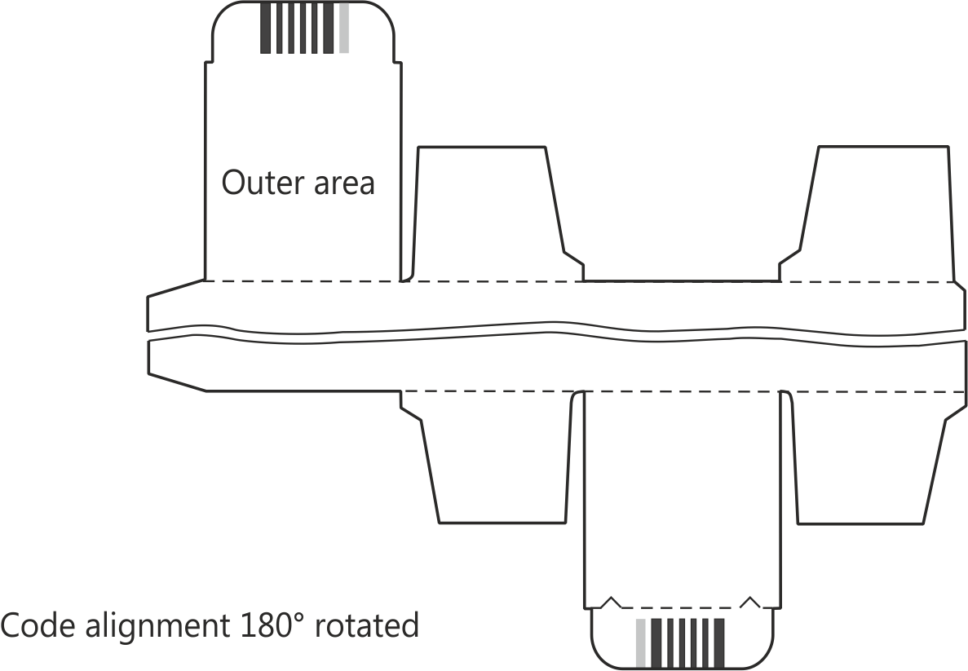
Two levels of coding
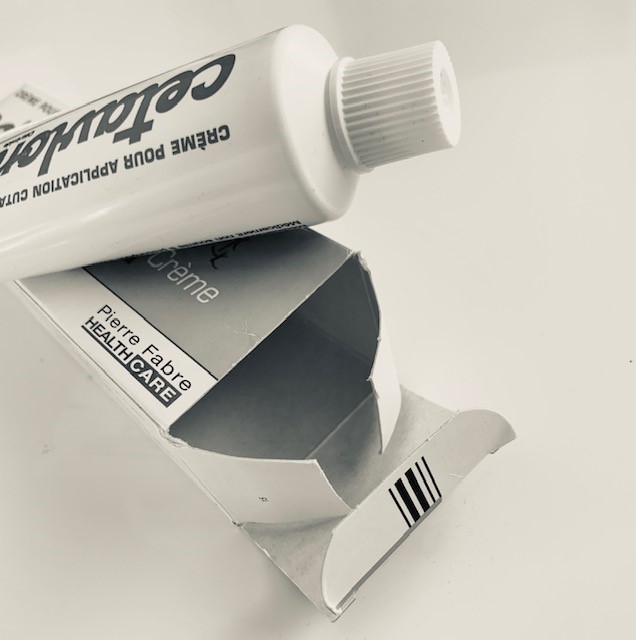
Although the number allocation is very simple, some PHARMA-CODE barcodes also use color to identify inserts and ensure they are included in package assembly. This difference could confuse and intimidate printers utilized in the automated production environment. How to make sure the printed barcodes are correct? Who is responsible for errors, why no compliance standard exists for PHARMA-CODE to control the application?
Like other barcodes, there is a PHARMA-CODE standard, but number allocation is entirely discretionary to the product manufacturer. The design provided to a contract printer includes barcode data that is part of an internal manufacturing process. Numbering errors or discrepancies are invisible and unknown to the printer. Manage remaining concerns with a simple contractual agreement, which absolves the contractor printer or packager of responsibility for label design data, including barcodes, in the customer-supplied file.
Still, there are print quality specifications and tolerances. Verification is unconventional but important. Best practices: deploy verifying cameras when the individual medicine carton is packed, inspecting the correctness of inserts to avoid recalls.
Familiar ISO print quality verification uses a red light source; barcodes are ideally black against a white substrate. To verify a multi-color PHARMA-CODE, a white light verifier is used. Special PHARMA-CODE software is also necessary.
Two levels of verification
Verification can also include validation. This is particularly true with PHARMA-CODE, which confirms the inclusion of only the correct collateral materials in the pharmaceutical package. Verifying the barcode is the perfect time to do this. Some verifiers can perform a lookup to a database. This matches the barcode to the product and assures packaging accuracy.
Beyond the significant differences between PHARMA-CODE and open-loop symbology, there are important similarities. Barcode quality is paramount: whatever the use case, the barcode must work. This series will delve more deeply into the PHARMA-CODE standard, quality attributes, and verification.
Continue to part 3 of our PHARMA-CODE series.
*Co-authored with John Nachtrieb, CEO of Barcode Test.